What is Porosity in Welding: Comprehending Its Causes and Enhancing Your Skills
What is Porosity in Welding: Comprehending Its Causes and Enhancing Your Skills
Blog Article
Porosity in Welding: Identifying Common Issues and Implementing Best Practices for Avoidance
Porosity in welding is a pervasive problem that frequently goes unnoticed until it causes significant issues with the integrity of welds. This usual flaw can jeopardize the strength and resilience of welded frameworks, posing safety risks and bring about expensive rework. By understanding the root triggers of porosity and executing reliable prevention techniques, welders can substantially enhance the top quality and reliability of their welds. In this discussion, we will explore the essential factors adding to porosity development, analyze its detrimental results on weld performance, and go over the most effective practices that can be adopted to minimize porosity incident in welding processes.
Typical Root Causes Of Porosity
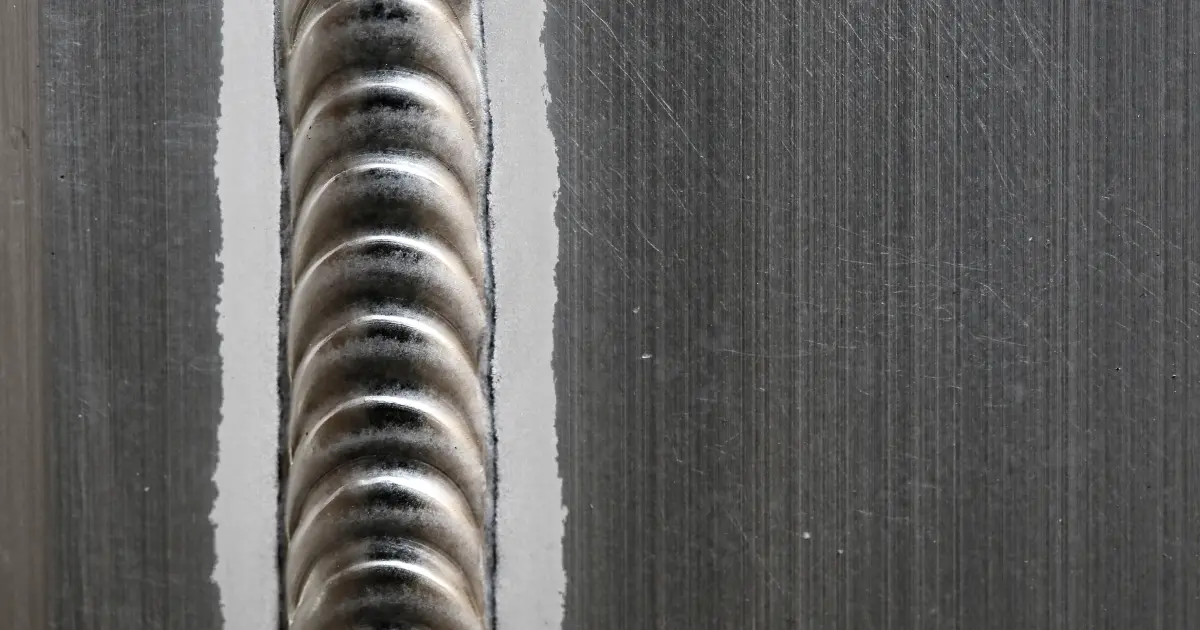
Utilizing filthy or damp filler products can present impurities into the weld, contributing to porosity problems. To minimize these common causes of porosity, comprehensive cleaning of base steels, correct shielding gas selection, and adherence to ideal welding specifications are crucial techniques in achieving top quality, porosity-free welds.
Effect of Porosity on Weld High Quality

The existence of porosity in welding can substantially jeopardize the structural integrity and mechanical properties of bonded joints. Porosity develops spaces within the weld metal, weakening its total stamina and load-bearing ability.
Welds with high porosity levels have a tendency to exhibit lower influence stamina and lowered capability to flaw plastically before fracturing. Porosity can hamper the weld's ability to successfully transmit pressures, leading to premature weld failing and prospective safety and security hazards in important frameworks.
Finest Practices for Porosity Avoidance
To boost the architectural stability and quality of bonded joints, what certain procedures can be applied to decrease the incident of porosity during the welding process? Using the proper welding strategy for the certain product being welded, such as changing the welding angle and gun position, can even more prevent porosity. Normal examination of welds and instant remediation of any concerns recognized throughout the welding process are necessary methods to stop porosity and generate high-grade welds.
Relevance of Correct Welding Methods
Implementing correct welding methods is paramount in making certain the architectural integrity and top quality of welded joints, building on the structure of efficient porosity prevention steps. Welding strategies directly impact the general strength and longevity of the welded framework. One crucial aspect of appropriate welding techniques is keeping the correct warm input. Excessive warmth can bring about enhanced porosity as a result of the entrapment of gases in the weld pool. Alternatively, inadequate warmth may lead to incomplete combination, developing prospective powerlessness in the joint. Additionally, utilizing the appropriate welding specifications, such as voltage, present, and take a trip speed, is vital for achieving sound welds with pop over to these guys marginal porosity.
In addition, the choice of welding process, whether it be MIG, TIG, or stick welding, ought to line up with the certain needs of the project to ensure optimal results. Appropriate cleansing and prep work of the base metal, in addition to picking the right filler material, are likewise necessary parts of proficient welding strategies. By sticking to these best techniques, welders can decrease the threat of view it porosity formation and produce top quality, structurally sound welds.

Checking and Quality Assurance Measures
Testing treatments are crucial to identify and protect against porosity in welding, making certain the toughness and resilience of the final item. Non-destructive screening techniques such as ultrasonic testing, radiographic screening, and aesthetic assessment are frequently used to determine potential problems like porosity.
Conducting pre-weld and post-weld examinations is likewise important in keeping quality assurance requirements. Pre-weld examinations entail verifying the materials, devices settings, and cleanliness of the workplace to stop contamination. Post-weld inspections, on the various other hand, assess the last weld for any type of defects, consisting of porosity, and confirm that it meets defined requirements. Implementing a thorough quality assurance plan that includes thorough screening procedures and evaluations is vital to decreasing porosity concerns and guaranteeing the total top quality of bonded joints.
Final Thought
Finally, porosity in welding can be an usual problem that impacts the high quality of welds. By identifying the typical sources of porosity and applying best methods for prevention, such as appropriate welding methods and screening actions, welders can make certain excellent quality and reliable welds. directory It is vital to focus on avoidance approaches to decrease the occurrence of porosity and maintain the integrity of welded structures.
Report this page